How to move material from Storage to production feed line
Most injection molders use a variety of plastic resin pellets which they store on-site. There are an assortment of storage options available depending on how many different plastic types are used and in what quantities. Probably one of the most common arrangements is stacked bags on a pallet, as many as 40-50 bags, with the pallets stacked two high. These bags are sealed against the environment and made of a tough material that is hard to puncture. They may also be shrink wrapped together in order to stabilize the load. At all steps of handling the plastic resin pellets, care must be taken not to puncture the container, leading to lost time and product while the spill is cleaned up.
If a facility uses pellets in larger quantities, then they may use bulk boxes, which have an internal reinforcement membrane to help make them puncture resistant. In certain cases, for much larger users, custom silos may be produced and stored on site either indoors or outdoors. Regardless of the scale of the operation, storage containers are intended to protect the resin pellets from the environment and also from being spilled. Regardless of the storage means, operators need to be alert to container damage, poorly sealed bags, or boxes that have tears or punctures. These need immediate correction. Transferring material from bags or boxes to small containers for day-to-day use is another point of risk for spillage. Often bags do not empty fully, or may have mechanical closures or valves that are faulty.
From a top level view, the contents of the storage bins should be at the right temperature and dew point to be delivered to the production injector or extruder. To ensure this is the case, once the pellets are ready for use they will likely be moved directly to a drying hopper. This will ensure that the temperature and the dew point are appropriate for the job being run.
As an example process, let’s assume, for simplicity that extruder speed will be used for control and that the feed hopper will be slightly overfed. Since we are producing for an environmentally sensitive customer we will also be using a percentage of regrind along with virgin material. This is a fairly common practice, so we’ll take a look at this as our baseline configuration and follow the journey of pellets to the finished product
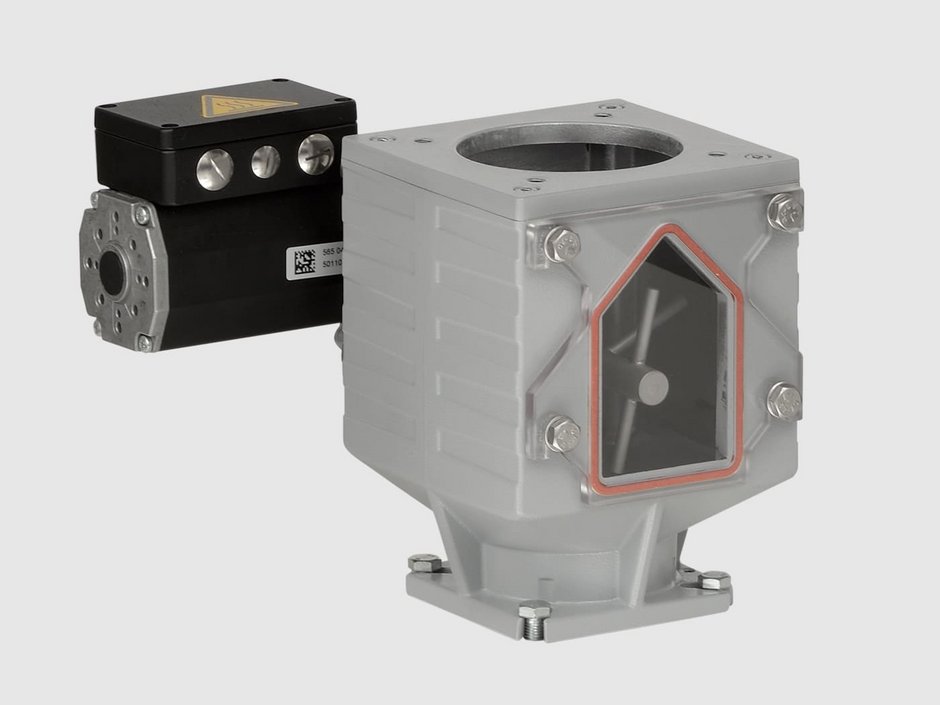
MIXING IT UP
Since we’re talking about a two-part mix for the production, a two-part proportioning valve could be used. Proportioning valves have two openings for the two materials, each with a controllable flap or piston, which acts as an on/off valve under gravity feed. Usually the motive force for the valves is pneumatic as compressed air is a readily available source of energy. The relative frequency of cycling between the two valves determines the percentage mix of virgin vs. regrind mix. In reality this results in different thicknesses of layers deposited in the hopper, which should become more homogeneous as it travels towards the production loader. In some cases a mixer is placed before the feed neck to provide a mechanical mixing to ensure a homogeneous mix. A mixer module in shown in the picture at right.
A dosing unit, would operate differently by maintaining a proportionate flow of the two different materials continuously. A dosing unit disperses the two materials usually very near the feed neck. Since the proportion is controlled, it doesn’t require much residence time in the feed hopper as you might require with proportionate valve control. Using a dosing unit also makes sense if the dosing medium is powder or liquid.
PELLETS ON THE MOVE
Speaking more generally, for a single type and color of plastic, used in bulk, it may be stored in very large bins or even silos external to the manufacturing facility. In that case, siloed pellets would be transported to a drying hopper inside the building, particularly if the manufacturing plant is situated in a highly humid part of the world. Desiccant dryers are most effective, especially so if the inside of the factory can be kept at a constant temperature and humidity. From there it may be dispensed into big bags, or daily bins depending on the day’s planned usage rate. From a big bag or daily bin, the pellets may need to go to a dosing unit for blending with a colorant, plasticizers, or even glass beads or fibers. The resultant product may be ready to go into the production hopper, or it may need a little time in a vacuum tank to lower the dew point. When the weight and dew point are right, it’s ready to go into the production hopper to start making parts.
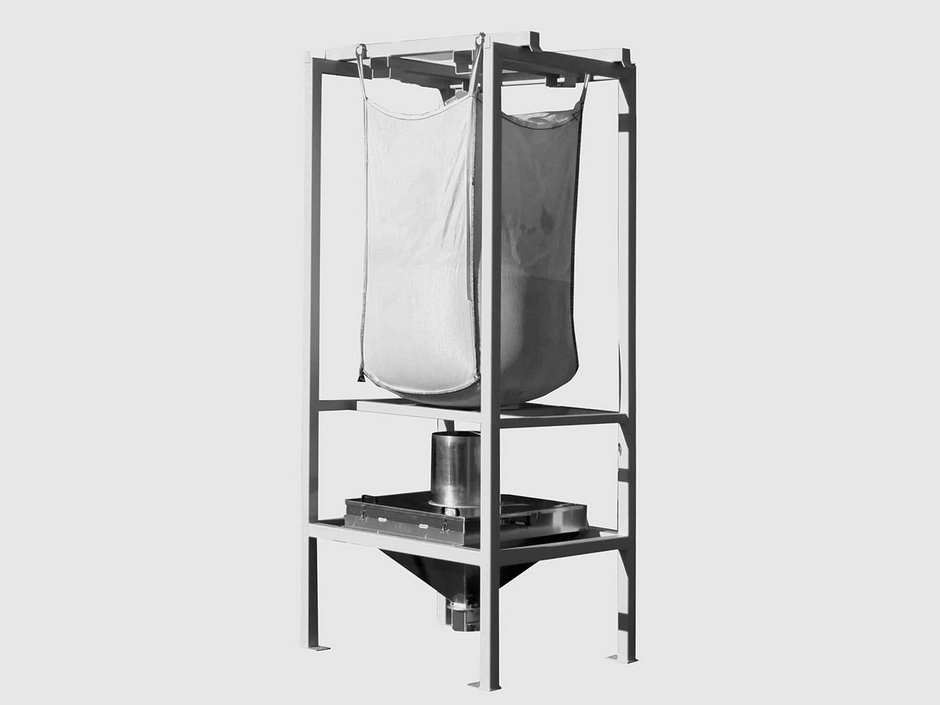
MULTIPLE FLOW STREAMS?
A third scenario is the use of the same starting resin, but with different treatments to end up with multiple products of different colors, physical characteristics, or percent of regrind. From the stage when the pellet is inside the building and at the right temperature and humidity, it may need to travel to several different stations for different treatments. Depending on the amount of material being handled it may be possible to gravity feed from a big bag into smaller containers, with each container going through different stages inside different dosing units. If the quantity is large enough it may make sense to have the plant designed around a central dispensing station. In that case, fixed piping needs to be installed and routed to a central location.
There are manual and automatic systems available to allow an operator to connect one source of pellets to multiple destinations. These systems often have sensors to indicate that they are connected to the correct production machine. Pellets are moved via a vacuum system for ease of conveyance. Using a central location and vacuum conveying has its own special requirements. Whether your requirements are straightforward, or require multiple steps, the challenge is to keep all materials at the right temperature, humidity and being fed at the appropriate rate. At the same time, operators need to be on the lookout for potential problems when handling resin pellets. An experienced crew works together like a well-oiled machined to produce high quality and consistent product every step of the way.