Optimizing the Drying Cycle for Plastics
When it comes to plastics, most people assume that they are “waterproof”- meaning they will shed water without absorbing any. In reality, most plastics consist of long-chain polymers, which are slightly polarized. Since water is also slightly polarized, plastics do have a tendency to absorb water to varying degrees. If something has absolutely no affinity for water at all it is referred to as hydrophobic and if it has some affinity for water it is hygroscopic. Plastics vary pretty widely in their ability to absorb water: from a low of about 0.07% moisture up to a high of 9%. Excess water can lead to surface discoloration of the molded plastic product. In more extreme cases the water will combine chemically with the plastic, a process called hydrolysis cause it to breakdown structurally. Regardless, controlling the moisture, through drying plastics prior to melting and injecting is a necessary part of the overall process.
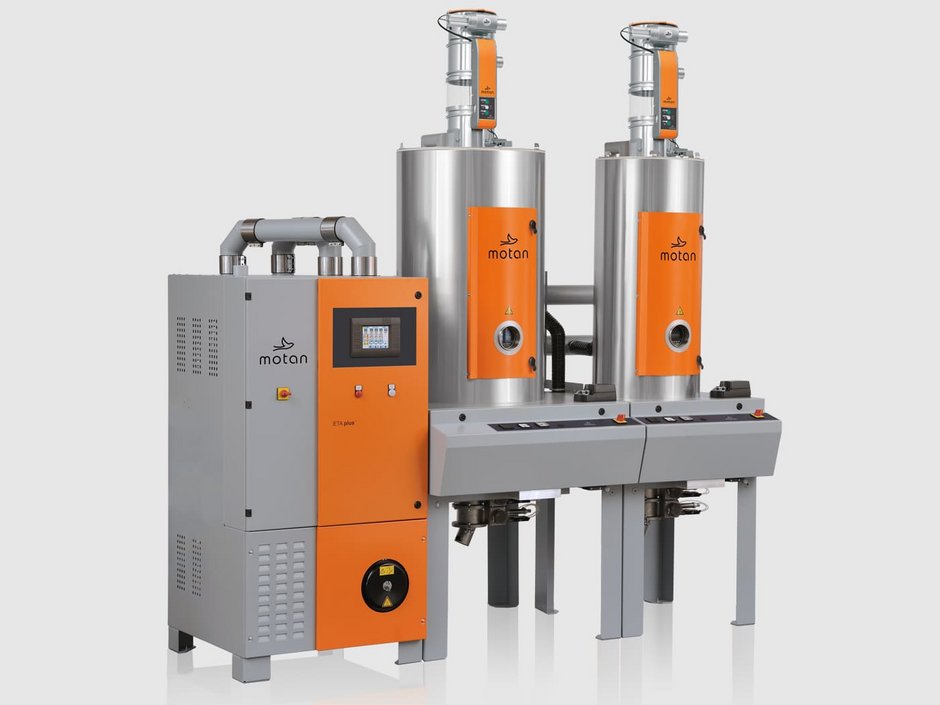
CONSIDERATIONS DUE TO PROCESSING
It might seem straightforward to just completely dry all plastic pellets down to a fractional percent of moisture, but that would be oversimplifying and in the case of hydrophobic plastics it could be wasting energy with no net benefit. It is not unusual for plastic blends to be used in injection molding. In that case the moisture sensitivity of the most sensitive plastic in the blend must be the deciding factor in how dry the mixture needs to be before it can be used. For mildly hygroscopic plastics whose only concerns are cosmetic, a percentage in the range of 0.05 to 0.10% moisture should be sufficient in most cases. However, for those plastics that are prone to hydrolysis, percentages need to be below 0.02% and some as low as 0.005%. The degree of moisture “contamination” is also affected by the melt temperature and the amount of time it is expected to be in a liquid state. Also, secondary operations such as ultrasonic welding and plating may figure into the overall temperature/moisture profile during fabrication.
METHODS OF DRYING
Another way of expressing the moisture in the plastic feedstock is dew point. This is the temperature at which the moisture in the plastic feedstock hopper would start to condense out of the air. The lower the temperature, then the lower the moisture content. For reference typical ambient dewpoints in the mid latitudes might range from -20˚F to +70˚ F. Typical dew points specified my manufacturers of the plastic feedstock are in the range of -20˚F to -40˚ F. There are several techniques available to dry out the plastic pellets in an injection molding operation. Desiccant dryers contain a water-absorbent material that can extract moisture to a very high degree. Typically compressed air is injected into a desiccant chamber to remove the moisture from the air This compressed, dry air then passes over the plastic feed hopper, extracting moisture from that container. Eventually the desiccant will get saturated and need regeneration. This can be achieved by circulating warm compressed air through the desiccant chamber to extract excess moisture. Of course we are all familiar with the fact that hot air on its own has a drying effect, however the temperature needed for these low dew points can get dangerously close to the melt temperature of the feedstock, so the presence of desiccants is almost always part of these types of drying systems as it can extract moisture at a lower temperature.
Another common method for drying is called vacuum drying and it is pretty much what you might think. The plastic feed stock typically will go through two stages of moisture extraction with the first stage using heat to drive off moisture and the second stage using a vacuum to take advantage of a lower evaporative pressure of water at lower pressures. There are also compressed air systems which are useful for drying small batches. They used air that has been compressed and then expanded to reduce the dew point. This requires maintaining clean dry air and can achieve dew points in the -20˚F range.
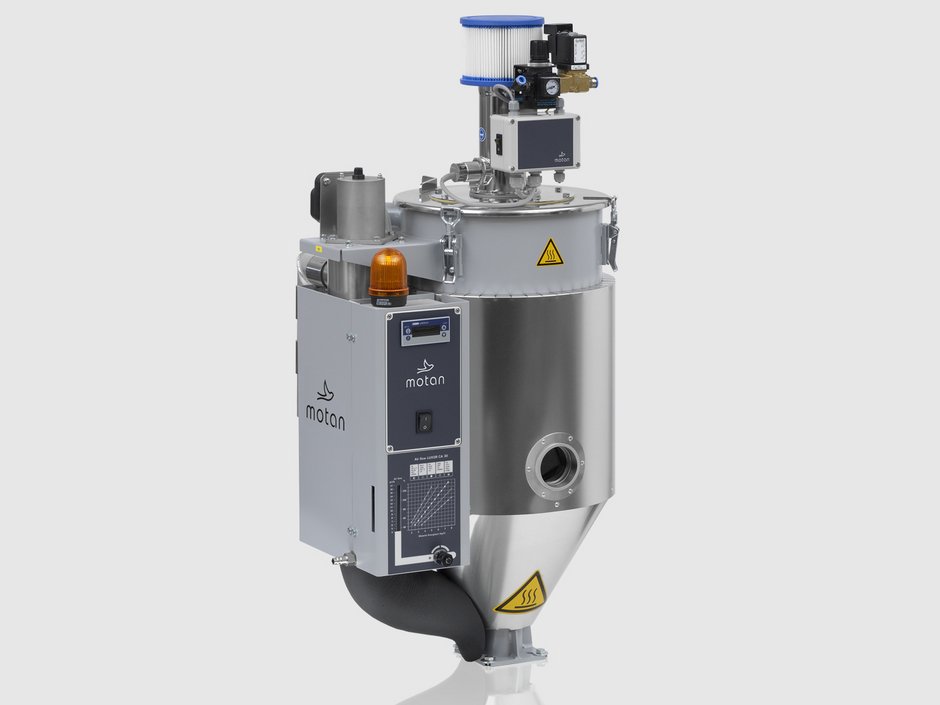
HOW TO EFFECTIVELY MEASURE MOISTURE CONTENT
As we have seen, achieving the right low moisture content is critical to clean plastic molded parts. It is also important to follow the manufacturer’s recommendations on moisture level and melt temperatures. All of which begs the question, how do we know that the correct dew points are being achieved and properly measured in the process? The simplest (and least accurate) method is to take the weight of a measured sample and heat it up for a specified period of time. The heat drives off the volatile components of the sample, reducing its weight.
The problem with this method is that plastics often have additives and other volatile components that will outgas when heated so the weight loss measured includes not only water but other volatile compounds as well. An improvement of this process is to follow the same procedure, but perform the test in a controlled chamber which is backfilled with dry nitrogen. By analyzing the gas content the water portion can be separated out from the other volatiles and a more accurate reading is obtained.
Since the process of drying and measuring the change in weight of a sample is a time consuming process this industry is evolving different moisture sensing techniques. Most commonly the dielectric properties of plastic vary with moisture content giving a direct measure of the moisture content of a specific sample. The measurement is immediate and it is a direct measurement of the moisture content of the plastic. The lost weight method, first mentioned is a measurement technique that a lot of injection molders are familiar with. Which ever method is chosen depends on the experience and reliability of the test, the operator, the plastic being used and the batch sizes.
IN SUMMARY
Clearly, we have seen the critical nature of managing the moisture content in plastic molding operations. This ends up being a delicate balancing act between drying temperature, air-flow, dew-point temperature and the drying time. Fortunately, reliable and well calibrated equipment is available from Motan to help you with getting the balance just right
CONSIDERATIONS DUE TO PROCESSING
It might seem straightforward to just completely dry all plastic pellets down to a fractional percent of moisture, but that would be oversimplifying and in the case of hydrophobic plastics it could be wasting energy with no net benefit. It is not unusual for plastic blends to be used in injection molding. In that case the moisture sensitivity of the most sensitive plastic in the blend must be the deciding factor in how dry the mixture needs to be before it can be used. For mildly hygroscopic plastics whose only concerns are cosmetic, a percentage in the range of 0.05 to 0.10% moisture should be sufficient in most cases. However, for those plastics that are prone to hydrolysis, percentages need to be below 0.02% and some as low as 0.005%. The degree of moisture “contamination” is also affected by the melt temperature and the amount of time it is expected to be in a liquid state. Also, secondary operations such as ultrasonic welding and plating may figure into the overall temperature/moisture profile during fabrication.
METHODS OF DRYING
Another way of expressing the moisture in the plastic feedstock is dew point. This is the temperature at which the moisture in the plastic feedstock hopper would start to condense out of the air. The lower the temperature, then the lower the moisture content. For reference typical ambient dewpoints in the mid latitudes might range from -20˚F to +70˚ F. Typical dew points specified my manufacturers of the plastic feedstock are in the range of -20˚F to -40˚ F. There are several techniques available to dry out the plastic pellets in an injection molding operation. Desiccant dryers contain a water-absorbent material that can extract moisture to a very high degree. Typically compressed air is injected into a desiccant chamber to remove the moisture from the air This compressed, dry air then passes over the plastic feed hopper, extracting moisture from that container. Eventually the desiccant will get saturated and need regeneration. This can be achieved by circulating warm compressed air through the desiccant chamber to extract excess moisture. Of course we are all familiar with the fact that hot air on its own has a drying effect, however the temperature needed for these low dew points can get dangerously close to the melt temperature of the feedstock, so the presence of desiccants is almost always part of these types of drying systems as it can extract moisture at a lower temperature.
Another common method for drying is called vacuum drying and it is pretty much what you might think. The plastic feed stock typically will go through two stages of moisture extraction with the first stage using heat to drive off moisture and the second stage using a vacuum to take advantage of a lower evaporative pressure of water at lower pressures. There are also compressed air systems which are useful for drying small batches. They used air that has been compressed and then expanded to reduce the dew point. This requires maintaining clean dry air and can achieve dew points in the -20˚F range.
HOW TO EFFECTIVELY MEASURE MOISTURE CONTENT
As we have seen, achieving the right low moisture content is critical to clean plastic molded parts. It is also important to follow the manufacturer’s recommendations on moisture level and melt temperatures. All of which begs the question, how do we know that the correct dew points are being achieved and properly measured in the process? The simplest (and least accurate) method is to take the weight of a measured sample and heat it up for a specified period of time. The heat drives off the volatile components of the sample, reducing its weight. The problem with this method is that plastics often have additives and other volatile components that will outgas when heated so the weight loss measured includes not only water but other volatile compounds as well. An improvement of this process is to follow the same procedure, but perform the test in a controlled chamber which is backfilled with dry nitrogen. By analyzing the gas content the water portion can be separated out from the other volatiles and a more accurate reading is obtained. Since the process of drying and measuring the change in weight of a sample is a time consuming process this industry is evolving different moisture sensing techniques. Most commonly the dielectric properties of plastic vary with moisture content giving a direct measure of the moisture content of a specific sample. The measurement is immediate and it is a direct measurement of the moisture content of the plastic. The lost weight method, first mentioned is a measurement technique that a lot of injection molders are familiar with. Which ever method is chosen depends on the experience and reliability of the test, the operator, the plastic being used and the batch sizes.
IN SUMMARY
Clearly, we have seen the critical nature of managing the moisture content in plastic molding operations. This ends up being a delicate balancing act between drying temperature, air-flow, dew-point temperature and the drying time. Fortunately, reliable and well calibrated equipment is available from Motan to help you with getting the balance just right