CONSIDERATIONS FOR PLASTIC DRYING
One of the most critical elements to a successful injection molding process is the water content of the plastic being injected into the mold. Excess moisture can create unwanted surface features on the finished molded part. Also in more extreme cases, moisture can cause structural weakness in the part. The level of dryness of the raw plastic is expressed either in terms of relative humidity or, more commonly, as dew point. The dew point being the temperature at which moisture condenses out of the air and on to the surfaces of the granulate. Though the two terms are related, relative humidity is an indication of how close to saturation the atmosphere is while dew point is a better indicator of moisture content.
To achieve this level requires a controlled balancing act involving four distinct variables. Drying temperature is one of the primary variables to control when attempting to dehumidify the raw material. In general, higher temperatures are better, however the operator must be careful not to get too close to the glass transition temperature which could lead to partial melting. Another contributor to achieving the desired dew point is airflow. This helps ensure that warm air is more easily distributed along the surface of the granulate being dried. Too high an air flow can fluidize the bed leading to over drying. High airflow speeds can also be costly to produce, so the trick is use only enough dry airflow to get the job done in a reasonable time. When using airflow, once the granulate has reached the desired dew point, there is little to no value in using heated air. It is easier to maintain a fixed dewpoint using dry air only and saves the cost of generating heat. Finally drying time will be a function of all of the elements mentioned above and the material that is being dried. Ideally the drying time is a short as possible within the limits of the material being used as longer drying periods can lead to costly over drying or partial melting, which should be avoided. Typical drying times might be in the range of four hours for hygroscopic formulations. The main types of equipment processes used in drying are: hot air, desiccant, pressure drying, or vacuum drying.
HOT AIR DRYING
Most drying techniques utilize convection methods to dry materials. The primary objective is to create a series of convective cells that circulate warm air over the surface of the granulate, carrying away any surface moisture generated during the process. Hot air drying, for instance, employs ambient air as the source and is best suited for drying plastics that are non-hygroscopic to slightly hygroscopic. However, the effectiveness of the hot air source is dependent on weather and seasonal conditions. This drying technique is ideal for pre-warming materials and removing surface moisture. For smaller amounts of granulate or micro granulate, there are drying cabinets that use the hot air principle. These cabinets contain the material to be dried in a series of trays, with hot air blown across the trays to extract moisture. They can also be used to maintain a small amount of material at the right humidity until it's ready for use.
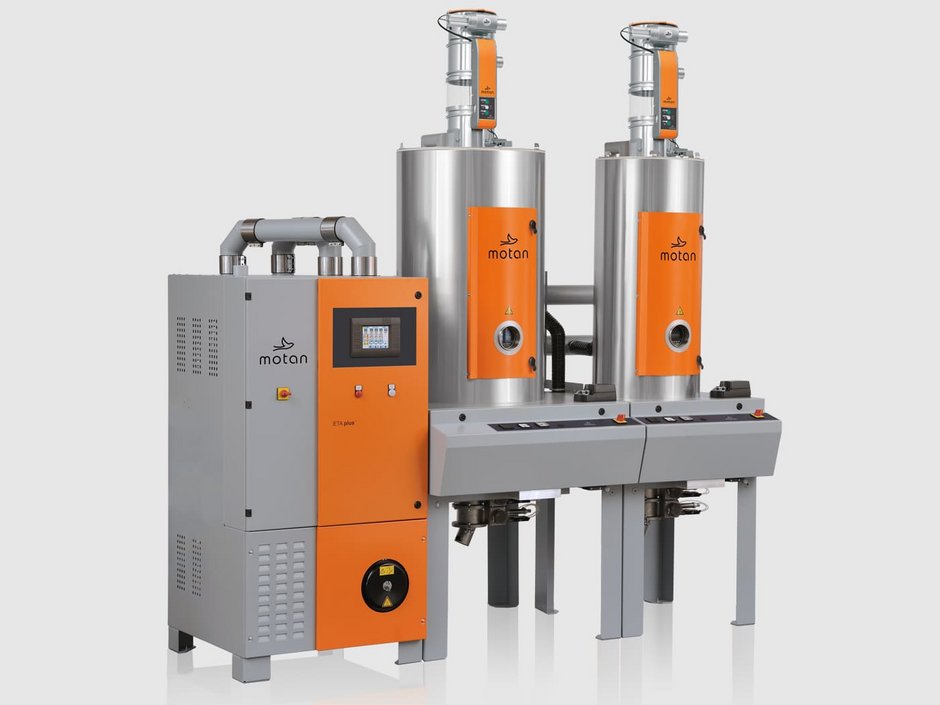
DESICCANT DRYING
Desiccant or dehumidifier dryers are the most widely used and consistent drying equipment for all plastics, setting the "gold standard" for achieving a specific dew point. The general principle of this method is a closed-loop control, where incoming hot air is already dehumidified using a desiccant. This dry air extracts moisture from the granulate in the drying bin and carries it to another stage that extracts the water from the air using a desiccant. In a separate stage, the desiccant is regenerated to remove any captured water. Meanwhile, the dehumidified air continues its loop through the drying bin to pick up another bit of moisture from the granulate. It's important to note that the desiccant works through a process known as adsorption, meaning that it will hold on to water molecules within a certain temperature range. If the desiccant is heated above its adsorption range, it will release its trapped moisture back to the atmosphere. Therefore, managing the temperature of the desiccant along with the airflow is an integral part of the process.
COMPRESSED AIR DRYING
H2 compressed air drying is a process that relies on a few key principles to effectively dry compressed air. The process begins by expanding compressed air to ambient pressure, which in turn reduces the dew point. The air is then heated in a dryer, causing it to absorb excess moisture that is then exhausted from the dryer. In some cases, the air is compressed and pre-expanded prior to entering the drying system. However, since producing large quantities of dry, clean, and oil-free compressed air is expensive, this process is typically best suited for small batch sizes. The process relies on ambient air, which limits its effectiveness in achieving low dew points (typically around +10˚C to -10˚C depending on weather conditions). Filters and membranes can be inserted at the compressed air entrance to achieve lower dew points, although this approach requires high-quality and reliable compressed air infrastructure. Despite its limitations, H2 compressed air drying is a convenient and straightforward method to achieve the desired dryness in compressed air.
VACUUM DRYING
This drying method is suitable as a batch process and relies on the principle that reducing air pressure decreases the boiling point of water, which drives moisture out of the granulate. Vacuum drying occurs in three stages. The first stage involves heating the granulate to help drive off moisture. This is followed by a vacuum stage where the amount of vacuum is steadily increased for approximately 20 minutes, further driving off moisture as vapor that gets extracted from the vacuum. The granules then move to the third chamber where they are discharged into a holding bin, and the process starts over again. Typical vacuum dryers can process around 200 pounds per hour.